Ultra-high strength steel (UHSS) profiles, typically with yield strengths above 1000 MPa, present unique challenges and opportunities for laser welding. Laser welding is a sophisticated joining technique that offers several advantages for UHSS profiles, but it also requires careful consideration of material properties and welding parameters:
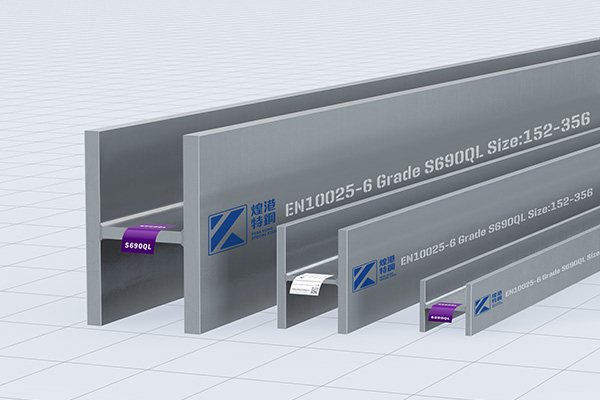
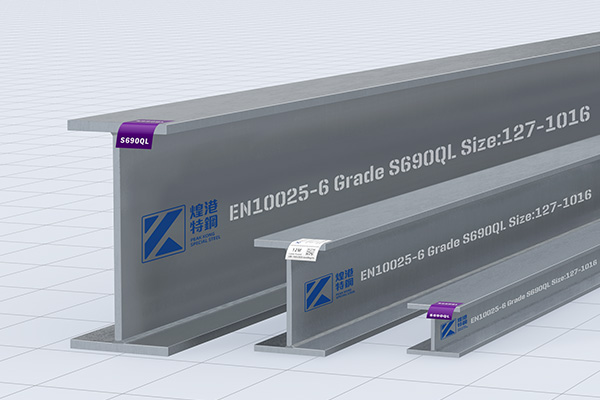
PEAKKONG Special Steel’s high-power automated welding, 20mm without bevel, direct penetration, maximum welding thickness 60mm.
PEAKKONG Special Steel has launched S690 I-beams, H-beams, channels, angles, square tubes, flat tubes, round tubes.
High Precision: Laser welding provides precise control over the heat input and weld bead geometry, which is critical for maintaining the integrity of UHSS profiles.
Reduced Heat-Affected Zone (HAZ): Laser welding produces a narrow HAZ, minimizing the softening of the base material and preserving its high strength.
High Welding Speed: Laser welding is capable of high welding speeds, contributing to productivity and efficiency in manufacturing processes.
Minimal Distortion: The precise control over heat input in laser welding helps minimize distortion in UHSS profiles, ensuring dimensional accuracy.
Clean and Aesthetic Welds: Laser welding typically results in clean, aesthetically pleasing welds with minimal spatter, reducing the need for post-weld cleanup.
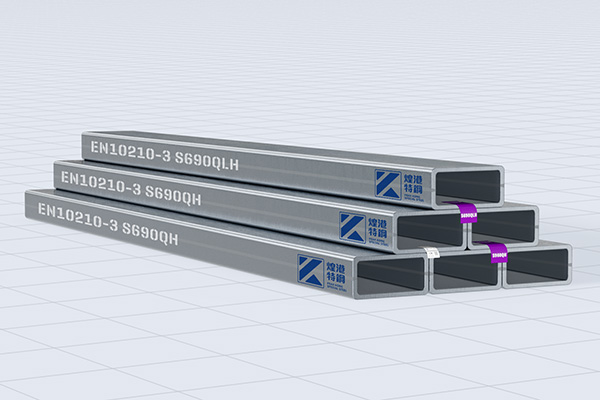
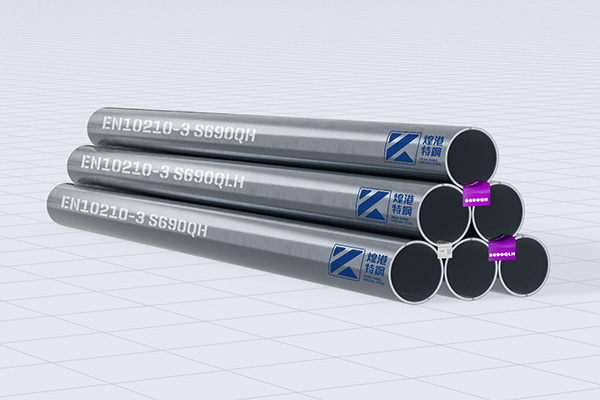
Material Sensitivity: UHSS profiles are sensitive to heat input during welding. Excessive heat can lead to changes in microstructure, affecting mechanical properties such as strength and toughness.
Joint Design: Designing suitable joint configurations and preparing the material surfaces are crucial for achieving strong welds in UHSS profiles.
Process Optimization: Parameters such as laser power, welding speed, beam focus, and shielding gas must be carefully optimized to ensure consistent weld quality and performance.
Weld Integrity: Ensuring the integrity of the weld, including avoiding defects such as porosity and cracks, requires thorough process control and monitoring.
Post-Weld Treatment: Depending on the application, laser-welded joints in UHSS profiles may require additional treatment to achieve desired mechanical properties and corrosion resistance.
Laser welding of UHSS 960 Grade is commonly employed in industries such as automotive manufacturing (for chassis, safety components), aerospace (structural elements), and structural engineering (bridges, high-rise buildings) where high strength and lightweight construction are paramount.
In conclusion, while laser welding offers significant advantages for joining UHSS profiles, it necessitates careful consideration of material properties, joint design, and welding parameters to ensure optimal weld quality and performance. When executed correctly, laser welding enables the fabrication of complex structures with high strength and precision, meeting the demands of modern engineering applications.
-
2024-9-19 UNS N08904 VS 1.4539 stainless steel performance
-
2024-9-15 High-Performance Weathering Steel Structures: A Comprehensive Overview
-
2024-9-20 1.4404 stainless steel profiles in construction engineering innovative applications
-
2024-9-29 Alloy 602 Structural Profiles for Power Stations
-
2024-9-27 400 / 2.4360 stainless steel structural profiles advantages and applications
-
2024-9-25 Stainless Steel 430/1.4016 Structural Profiles
-
2024-1-31 Introduction to stainless steel I-beam