Stainless steel types 1.4401 and 1.4404 are also known as grades 316 and 316L respectively. Grade 316 is an austenitic grade second only to 304 in commercial importance.
316 stainless steel contains an addition of molybdenum that gives it improved corrosion resistance. This is particularly apparent for pitting and crevice corrosion in chloride environments.
316L, the low carbon version of 316 stainless steel, is immune to grain boundary carbide precipitation (sensitisation). This makes it suited to use in heavy gauge (over about 6mm) welded components.
For elevated temperature applications the high carbon variant, 316H stainless steel and the stabilised grade 316Ti stainless steel should be employed.
The austenitic structure of 316 stainless steel gives excellent toughness, even at cryogenic temperatures.
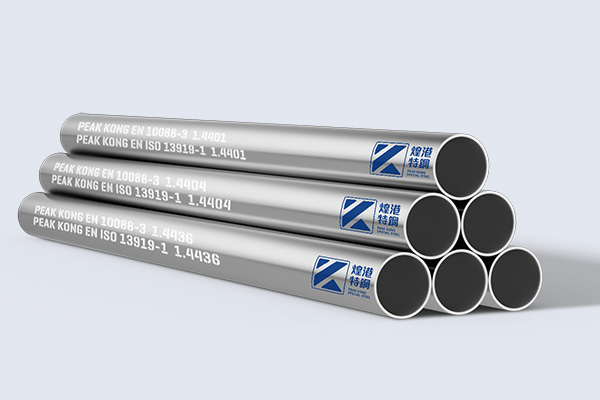
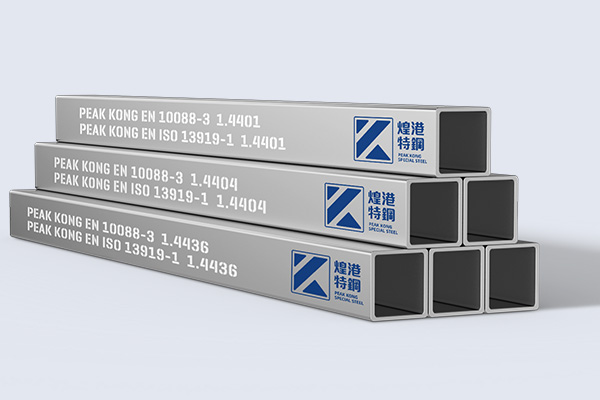
Property data given in this document is typical for bar and section products covered by EN 10088-3:2005. ASTM, EN or other standards may cover all products sold. It is reasonable to expect specifications in these standards to be similar but not necessarily identical to those given in this datasheet.
Stainless steel grade 316Ti contains a small amount of titanium. Titanium content is typically only around 0.5%. The titanium atoms stabilise the structure of the 316 at temperatures over 800°C. This prevents carbide precipitation at the grain boundaries and protects the metal from corrosion. The main advantage of 316Ti is that it can be held at higher temperatures for a longer period without sensitisation (precipitation) occurring. 316Ti retains physical and mechanical properties similar to standard grades of 316.
Chemical Element | % Present |
---|---|
Carbon (C) | 0.0 – 0.03 |
Chromium (Cr) | 16.50 – 18.50 |
Molybdenum (Mo) | 2.00 – 2.50 |
Silicon (Si) | 0.0 – 1.00 |
Phosphorous (P) | 0.0 – 0.05 |
Sulphur (S) | 0.0 – 0.03 |
Nickel (Ni) | 10.00 – 13.00 |
Manganese (Mn) | 0.0 – 2.00 |
Nitrogen (N) | 0.0 – 0.11 |
Iron (Fe) | Balance |
Physical Property | Value |
---|---|
Density | 8.0 g/cm³ |
Melting Point | 1400 °C |
Thermal Expansion | 15.9 x10^-6 /K |
Modulus of Elasticity | 193 GPa |
Thermal Conductivity | 16.3 W/m.K |
Electrical Resistivity | 0.74 x10^-6 Ω .m |
Nickel (Ni) | 10.00 – 13.00 |
Manganese (Mn) | 0.0 – 2.00 |
Nitrogen (N) | 0.0 – 0.11 |
Iron (Fe) | Balance |
Mechanical Property | Value |
---|---|
Proof Stress | 200 Min MPa |
Tensile Strength | 500 to 700 MPa |
Elongation A50 mm | 40 Min % |
Hardness Brinell | 215 Max HB |
Stainless Steel Grade 1.4404/316L also corresponds to the following designations but may not be a direct equivalent:
UNS S31603
316S11
- Equal Sided Angles
- Unequal Sided Angles
- Unequal T-Profiles
- I Beams
- Channel, (parallel)
- H Profiles
- Plate
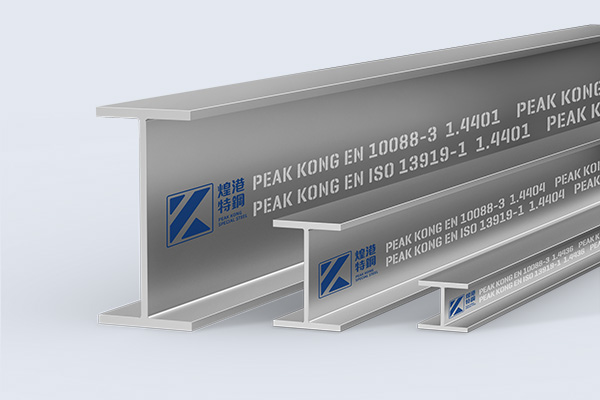
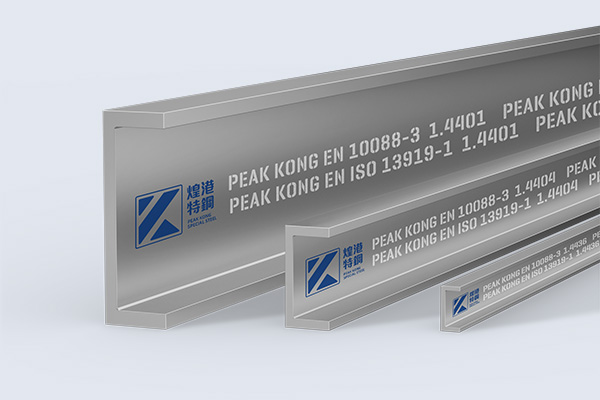
- Food processing equipment
- Brewery equipment
- Chemical and petrochemical equipment
- Laboratory benches & equipment
- Coastal architectural panelling
- Coastal balustrading
- Boat fittings
- Chemical transportation containers
- Heat exchangers
- Mining screens
- Nuts and bolts
- Springs
- Medical implants
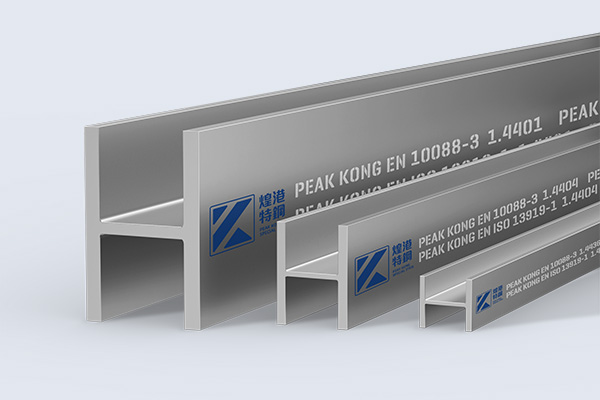
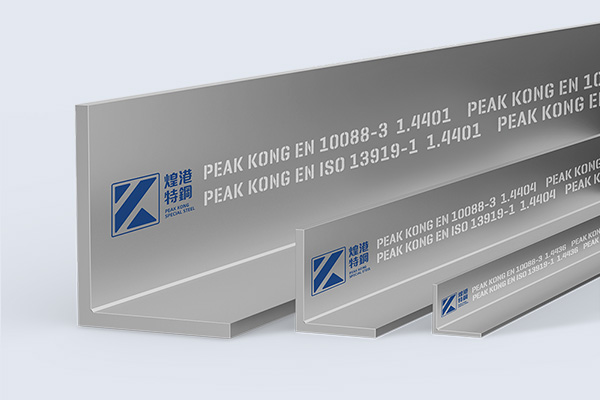
316 has good resistance to oxidation in intermittent service to 870°C and in continuous service to 925°C. However, continuous use at 425-860°C is not recommended if corrosion resistance in water is required. In this instance 316L is recommended due to its resistance to carbide precipitation.
Where high strength is required at temperatures above 500°C, grade 316H is recommended.
Fabrication of all stainless steels should be done only with tools dedicated to stainless steel materials. Tooling and work surfaces must be thoroughly cleaned before use. These precautions are necessary to avoid cross contamination of stainless steel by easily corroded metals that may discolour the surface of the fabricated product.
Grade 316 is readily brake or roll formed into a variety of parts. It is also suited to stamping, heading and drawing but post work annealing is recommended to relieve internal stresses.
Cold working will increase both strength and hardness of 316 stainless steel.
All common hot working processes can be performed on 316 stainless steel. Hot working should be avoided below 927°C. The ideal temperature range for hot working is 1149-1260°C. Post-work annealing is recommended to ensure optimum corrosion resistance.
- Cutting edges must be kept sharp. Dull edges cause excess work hardening.
- Cuts should be light but deep enough to prevent work hardening by riding on the surface of the material.
- Chip breakers should be employed to assist in ensuring swarf remains clear of the work.
- Low thermal conductivity of austenitic alloys results in heat concentrating at the cutting edges. This means coolants and lubricants are necessary and must be used in large quantities.
316 stainless steel cannot be hardened by heat treatment.
Solution treatment or annealing can be done by rapid cooling after heating to 1010-1120°C.
Fusion welding performance for 316 stainless steel is excellent both with and without fillers. Recommended filler rods and electrodes for 316 and 316L are the same as the base metal, 316 and 316L respectively. Heavy welded sections may require post-weld annealing. Grade 316Ti may be used as an alternative to 316 in heavy section welds.
Oxyacetylene welding has not been found to be successful for joining of 316 stainless steel.
-
2024-9-19 1.4539 stainless steel structural H profile
-
2024-9-29 N06025 Nickel-based alloy structural profiles
-
2024-9-16 Introduction to the performance of 2205 duplex stainless steel
-
2024-7-16 Properties of high-strength steel and advanced high-strength steel-Peak Kong Special Steel
-
2024-9-19 1.4462 stainless steel structural Beams and columns
-
2024-9-20 Application of Ti Gr 2 / 3.7035 structural profiles in marine industry
-
2024-9-27 Performance and application of 2.4360 stainless steel hollow structural profiles