Laser welding is particularly well-suited for joining advanced high-strength steel (AHSS) profiles due to its ability to provide precise control over the welding process. Here’s a detailed look at the performance aspects of laser welding AHSS profiles:
Peakkong Special Steel introduces S690 grade (H-beam, I-beam, channel, angle, square tube, flat tube, steel pipe) to the market.
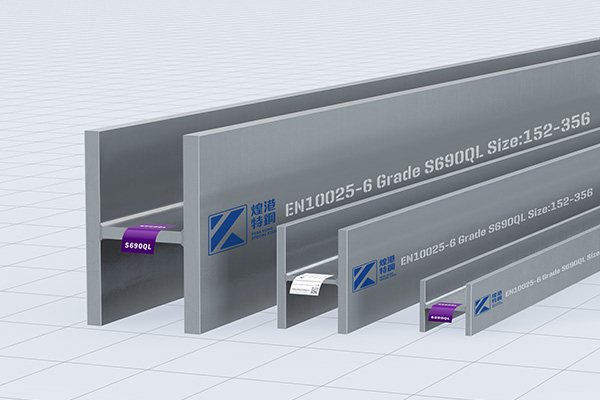
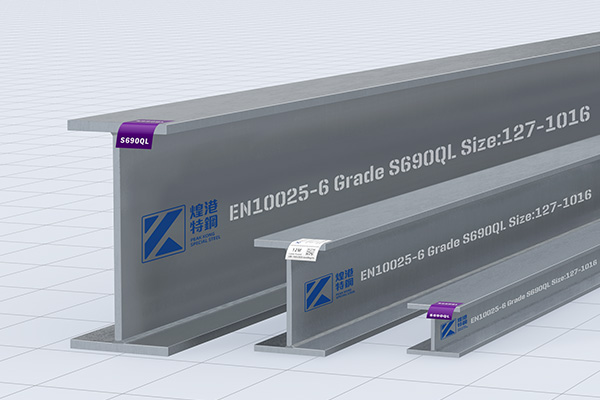
1. High Precision: Laser welding offers precise control over heat input, resulting in accurate and consistent weld bead geometry. This precision is crucial for maintaining the mechanical properties of AHSS, such as strength and ductility.
2. Reduced Heat-Affected Zone (HAZ): Laser welding produces a narrow HAZ compared to traditional welding methods like arc welding. This minimizes softening of the surrounding material and helps retain the high strength of AHSS.
3. High Welding Speed: Laser welding is capable of high welding speeds, contributing to increased productivity in manufacturing processes.
4. Minimal Distortion: The focused and controlled heat input of laser welding helps minimize distortion in AHSS profiles, ensuring dimensional accuracy and maintaining tight tolerances.
5. Versatility: Laser welding can accommodate various joint designs and thicknesses of AHSS profiles, providing flexibility in design and manufacturing.
6. Clean and Aesthetic Welds: Laser welding typically results in clean, aesthetically pleasing welds with minimal spatter, reducing the need for extensive post-weld cleanup.
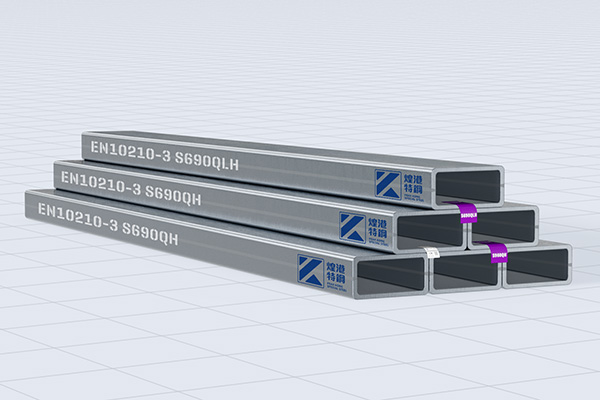
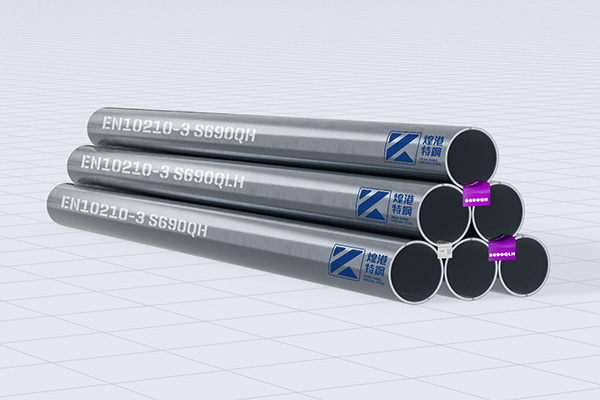
1. Material Sensitivity: AHSS is sensitive to heat input during welding. Careful control of laser parameters such as power, beam focus, and welding speed is necessary to avoid detrimental effects on the material’s microstructure and mechanical properties.
2. Joint Design: Designing appropriate joint configurations and preparing the material surfaces are critical for achieving strong and durable welds in AHSS profiles.
3. Process Optimization: Parameters such as laser power, welding speed, beam focus, and shielding gas must be optimized for each specific application to ensure consistent weld quality and performance.
4. Weld Integrity: Ensuring the integrity of the weld, including avoiding defects such as porosity and cracks, requires thorough process control and monitoring.
5. Post-Weld Treatment: Depending on the application, laser-welded joints in AHSS profiles may require additional treatment (e.g., stress relieving, surface finishing) to achieve desired mechanical properties and corrosion resistance.
Laser welding of AHSS profiles is widely used in industries such as automotive manufacturing (for chassis, safety components), aerospace (for structural elements), and structural engineering (bridges, high-rise buildings). It allows manufacturers to leverage the high strength and lightweight properties of AHSS while achieving precise and reliable welds.
In conclusion, laser welding offers significant advantages for joining AHSS profiles, including high precision, minimal heat input, and reduced distortion. By carefully optimizing welding parameters and adhering to best practices in joint design and process control, PEAKKONG Special Steel can achieve high-quality welds that meet the stringent performance requirements of modern engineering applications.
-
2024-9-29 Alloy 602 Structural Profiles for Power Stations
-
2024-9-16 What are some typical applications where 2205 and 1.4436 duplex stainless steels are used?
-
2024-9-27 C22 / 2.4602 Nickel-Based Alloy Hollow Structural Profiles
-
2024-9-21 Application of S960 steel in bridge engineering
-
2024-9-25 254SMO vs. UNS S31254 Super Stainless Steel for Structural Beams and Columns
-
2024-9-29 Alloy 602 CA / 2.4633/N06025 Nickel-based alloy structural profiles for beams and columns
-
2024-9-24 S690 Universal Columns Innovative applications in structural works